Poor waterproof performance
Comparation:Confirm whether the problem comes from the batch difference or comparison with other products.
No working fluid concentration: When critical concentration is used for wet feeding or dry feeding, improper operation will also lead to substandard waterproof effect.
Fabric type and color: Modified polyester, polypropylene and wool need special waterproof agent or specific formula
Liquid rolling rate: Fast setting speed and poor permeability are easy to cause uneven liquid on fabric.
With or without other additives: Hydrophilic and anionic substances will reduce the waterproof effect
Whether setting conditions are sufficient: If not, the waterproof effect will be affected
With or without calendering: Calendering will damage the film-forming performance of waterproof agent and reduce the waterproof effect
PH value of working fluid: The fixed fabric potential is affected by the pH value of working fluid, and it will affect the waterproof effect
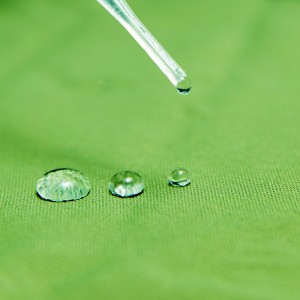
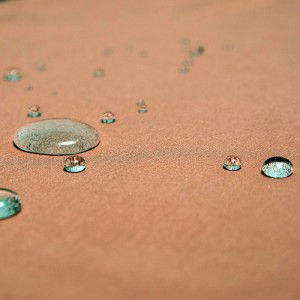
Waterproof spots and strips
With or without other additives: Check the stability of working fluid before processing.
External mechanical force: High speed mixing or strong pumping power is easy to demulsificate the waterproof agent.
Liquid rolling rate: Changing the amount of liquid will make the fabric surface uneven after drying
Big foam: When the foam is larger or more, it is easy to form insoluble bubbles, which attach to the fabric and form spots or strips after drying.
Fabric residue: During the processing, the residual additives on the surface fall off to cause the instability of the working fluid to form insoluble bubbles or demulsificate the working fluid
Attentions in processing
Control the PH value of working fluid at weak acid 4-6.
Clean the fabric surface without alkali and other surfactants.
High speed mixing or strong pumping power is easy to demulsificate the waterproof agent.
Compatible with cationic and nonionic additives. Test and confirm before use.
The working fluid concentration for wet feeding is higher than that in dry feeding.
Fast setting speed and poor permeability are easy to cause uneven liquid on fabric and reduce waterproof effect.
Water/oil repellent effect is reduced when the drying (accompany drying) temperature is below 140℃ for conventional waterproof agent.
When the pressure is too high during calendaring and the emulsifier in the waterproof agent seeps out, the waterproof effect will be reduced.
Too much foam is easy to form insoluble bubbles, which attach to the fabric and form the spots after drying.
Uneven liquid for coating after drying will cause unevenness of uncoated layer.
PP type non-woven fabric is not resistant to high temperature and requires low temperature waterproof agent.
Color is darkened during the waterproof processing.
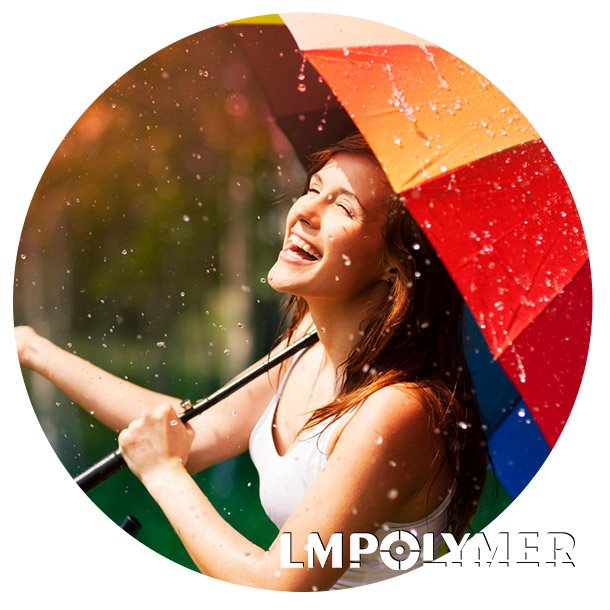